1. Scope of the coverage: |
This specification is pertinent to the application of insulated
0Ω resistors (designated as RZ). |
2 .Temperature range of the application: |
-55℃ ~ +155℃。 |
3. Type: |
The color of the coating resin for the 0Ω insulated
resistors is gray. |
4.Marking and illustration: |
Two types of designation methods are available for 0Ωinsulated
resistors. One is black ink |
alphanumeric marking and the other one is color code marking.
The criteria of using either one of |
the marking methods depend on the size of the resistors
and customers request which is listed in |
the following: |
alphanumeric marking ---->1/2W (Fig.1) |
color code marking ------------>1/6W、1/4W (Fig.2) |
|
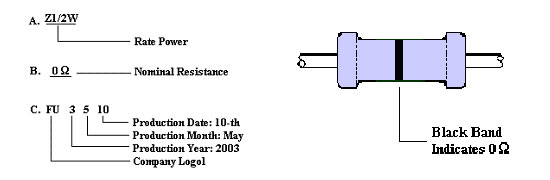 |
|
5.Dimension, voltage, resistance range: listed in
the following Table-1 |
Rated
power
(W) |
Type |
Resistance (Ω) |
2 |
J ( ±5%) |
L |
Dψ |
ι |
dψ |
1/6 |
Normal |
20mΩ以下 |
1.5A |
1.8±0.3 |
28±2 |
0.45±0.05 |
1/4 |
Normal |
20mΩ以下 |
2.5A |
2.4±0.1 |
28±2 |
0.60±0.05 |
1/2 |
Normal |
20mΩ以下 |
2.5A |
3.0±0.5 |
30±3 |
0.60±0.05 |
|
|
6.Coating |
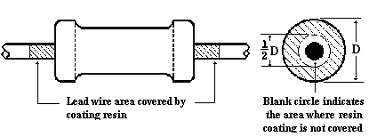 |
6.1 The body of the resistor is covered by nonflammable
silicon resin. |
6.2 The maximum length of the lead wire covered by the
resin is 2mm. |
6.3 The maximum area of the end cap which is not covered
by the resin is half of the diameter of |
6.3 the cap. |
6.4 The status of coating condition described by 6.2 and
6.3 are acceptable. |
|
7.Characteristics of electrical performance |
7.1 Rated power |
The rated power indicates the maximum power the resistor
can endure continuously when the |
ambient temperature is equal to or lower than 70℃. When
the ambient temperature is higher than |
70℃, the rated power of the resistor is determined by the
derating curve described in the following |
figure. |
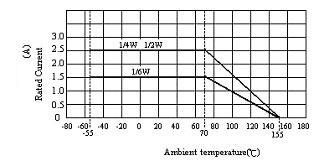 |
7.2 Dielectric strength (Ref. JIS C5202 5.7) |
Equipment: Dielectric strength tester |
The body of the resistor is wrapped around by the aluminum
foil without extending beyond the |
resistor body. Clap one electrode on the aluminum foil
and the other electrode on the lead wire. |
Apply following voltage from the tester to the resistor
for 1 min.. No flash-over, burning or |
breakdown should be observed. |
|
Wattage |
1/6W |
1/4W |
1/2W |
Voltage |
300V |
500V |
500V |
|
|
8.Environmental tests |
8.1 Load life test (Endurance with rated load) (Ref. JIS
C5202 7.10) |
Equipment: High temperature chamber and DC power supply |
The resistors are put in a fixture where no interference
will be allowed. Put the fixture in a 70±3℃ |
chamber and apply rated current in table-1 with a cycle
of 90 min. ON and 30 min. OFF for
|
hours. After 240, 480, 720 and 1,000 hours, the resistors
are taken out and stabilize at room |
temperature for 30 min. and then the resistance is measured.
Upon each step of resistance |
measurement, the change of the resistance should be≦20mΩ
and the appearance should show |
no remarkable abnormality and legibility of marking. |
|
8.2 Endurance under damp heat and load (Ref. JIS C5202
7.9) |
Equipment: Constant temperature and humidity chamber, DC
power supply |
The resistors are put in a fixture where no interference
will be allowed. Put the fixture in a 40±2℃ |
chamber with RH=90~95% and apply rated current in table-1
with a cycle of 90 min. ON and 30 |
min. OFF for hours. Water drops should avoid
dripping on the resistors. After 240 and |
1,000 hours, the resistors are taken out and stabilize
at room temperature for 1 hour and then the |
resistance is measured. Upon each step of measurement,
the change of the resistance should be |
≦20mΩ and the appearance should show no remarkable abnormality
and legibility of marking. |
|
8.3 Temperature cycling (Ref. JIS C5202 7.4) |
Equipment: High temperature chamber, low temperature chamber |
Put the resistor to -55℃ chamber for 30 min. then take
it out at room temperature for 2 to 3 min.. |
Put the resistor to +85℃ chamber for 30 min. then take
it out at room temperature for 2 to 3 min. |
This completes a cycle. Repeat the cycle 5 times. Put resistors
at room temperature for 90 min. |
and then measure the resistance. Compare the resistance
before and after test. The acceptable |
change of resistance is≦20mΩ. The appearance should show
no remarkable abnormality and |
legibility of marking. |
|
9.Mechanical performance |
9.1 Resistance to soldering heat (Ref. JIS C5202 6.4) |
Equipment: Solder bath |
Measure the resistance before the test. Immerse part of
the lead wire which is 4±0.8mm away |
from the body to the flux for 5 - 10 sec. Take the resistor
out and immerse resistors in the solder |
bath of 350±10℃ for 3.5±0.5 sec.. Stabilize at room temperature
for 1 hour and then measure the |
resistance value. Compare the resistance values before
and after the test, The acceptable change |
is ≦20mΩ. |
|
9.2 Solderability (Ref. JIS C5202 6.5) |
Equipment: Solder bath |
Immerse part of the lead wire which is 4±0.8mm away from
the body to the flux for 5 - 10 sec. Take |
the resistor out and immerse resistors in the
solder bath of 245±5℃ for 3.5±0.5 sec. Take the |
resistor out and inspect the lead wire visually. The acceptable
level is the coverage of the new |
solder to be 95%. The composition of the solder bath is
99.7% tin and 0.3% Cu. |
|
9.3 Robustness of terminals (Ref. JIS C5202 6.1) |
9.3.1 Tensile strength of termination |
Equipment: Weight gauge |
Fixed the resistor and apply axially along the lead wire
of 2.5Kg (0.8φ lead wire) , 1.0Kg (0.6φ lead |
wire) or 0.5Kg (0.45φ lead wire) for 30 sec.. The lead
wire should not break or detached from the |
resistor and the change of the resistance should be ≦20mΩ. |
|
9.3.2 Torsional strength |
Equipment: Torsion tester |
Bend the terminal 6.4mm away from the body according to
Fig-a to 90 degree with a curvature of |
0.75mm~0.80mm. The lead wire should be clamped at a point
of 1.2mm away from the bending |
point by a fixture which can rotate 360 degree according
to Fig-b. Rotate the resistor 360 degree |
clockwise and counter clockwise for 1 cycle. The rotation
speed is 360 degree per 5 sec.. Perform |
3 cycles for the lead wire diameter of 0.8φ, 1.5 cycles
for that of 0.6φ or 1 cycle for 0.45φ. The |
terminal should not break down or detached from the body.
The acceptable change of resistance |
is ≦20mΩ. |
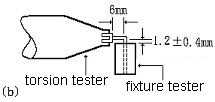 |
|